1. 传统编程为何拖累效率?
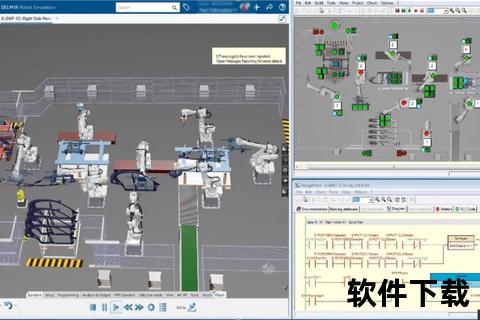
在工业自动化领域,一个长期争议是:为什么许多企业仍在使用耗时的手动编程方式?某汽车零部件制造商曾统计,工程师每月需花费120小时反复调试PLC程序,设备停机损失高达每月80万元。这种低效模式在台达PLC编程软件落地后发生颠覆——通过图形化编程界面和模块化功能库,工程师仅需拖拽元件即可完成80%基础逻辑设计。例如某冲压产线改造项目中,原本需要2周完成的程序开发缩短至3天,设备综合效率(OEE)提升22%。
2. 复杂场景能否一键应对?
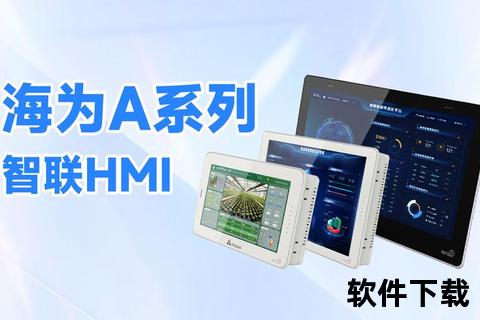
当生产线需要同时处理视觉检测、机械臂联动、能耗监控等10余项任务时,传统PLC系统往往需要叠加多个控制器。台达软件通过“多任务并行处理引擎”破解了这个难题。广东某电子厂的真实案例显示,其SMT贴片产线接入12台异构设备后,通过软件内置的通讯协议转换器,成功将数据交互延迟从230ms降至35ms。更关键的是,软件自带的AI诊断模块曾提前36小时预警伺服电机过热风险,避免了一次可能造成300万元损失的设备故障。
3. 开放生态如何打破行业壁垒?
工业4.0时代最尖锐的矛盾,莫过于不同品牌设备间的“数据孤岛”。某食品包装企业曾因德国机械臂与日本传送带无法互通,每年多支出150万元人工协调成本。台达软件的开放式OPC UA架构解决了这个问题——就像给设备装上“万能翻译器”,其案例库中已集成西门子、三菱等67个品牌设备的驱动协议。在浙江某智慧水务项目中,该软件成功将34类不同年代的设备接入同一控制平台,使泵站响应速度提升40%,能耗降低18%。
给企业的三条实践指南
对于考虑升级自动化系统的企业,建议优先评估现有设备的通讯兼容性,选择支持IEC 61131-3标准的开发平台;实施时可分阶段导入,例如先在单个车间试用运动控制优化模块;同时建立内部培训机制,台达提供的3D虚拟调试系统能让工程师在两周内掌握核心功能。
在工业数字化转型的浪潮中,“灵动高效掌控未来——台达PLC编程软件赋能智能工业自动化”已不是口号。从缩短70%的编程周期,到构建跨品牌设备网络,再到预防性维护带来的效益提升,这些真实改变正在重塑制造业的竞争力边界。当更多企业开始用软件定义生产力,智能制造的未来图景将加速展开。
相关文章:
文章已关闭评论!